Just how to Recognize What is Porosity in Welding and Improve Your Method
Just how to Recognize What is Porosity in Welding and Improve Your Method
Blog Article
Porosity in Welding: Identifying Common Issues and Implementing Ideal Practices for Prevention
Porosity in welding is a prevalent concern that usually goes undetected until it triggers significant troubles with the stability of welds. In this discussion, we will discover the vital variables contributing to porosity development, analyze its harmful results on weld efficiency, and talk about the ideal techniques that can be embraced to reduce porosity incident in welding processes.
Typical Reasons For Porosity
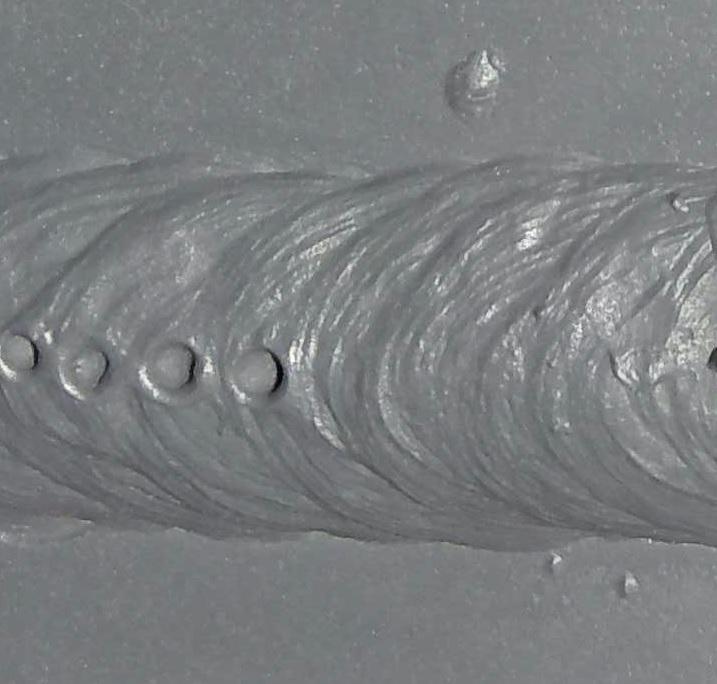
Using dirty or damp filler materials can present pollutants right into the weld, adding to porosity concerns. To alleviate these typical causes of porosity, comprehensive cleansing of base metals, appropriate shielding gas option, and adherence to optimal welding specifications are vital methods in attaining top quality, porosity-free welds.
Effect of Porosity on Weld Top Quality

The presence of porosity in welding can considerably jeopardize the architectural stability and mechanical residential properties of welded joints. Porosity produces voids within the weld steel, compromising its overall stamina and load-bearing capacity.
Welds with high porosity degrees have a tendency to show lower effect stamina and minimized ability to deform plastically before fracturing. Porosity can restrain the weld's capability to efficiently transmit pressures, leading to premature weld failing and potential security risks in important frameworks.
Finest Practices for Porosity Prevention
To enhance the architectural integrity and quality of bonded joints, what particular procedures can be executed to reduce the occurrence of porosity during the welding process? Porosity avoidance in welding is vital to guarantee the honesty and stamina of the final weld. One effective practice is proper cleaning of the base metal, eliminating any type of impurities such as corrosion, oil, paint, or wetness that could bring about gas entrapment. Making certain that the welding devices is in excellent problem, with tidy consumables and proper gas circulation rates, can also significantly decrease porosity. Furthermore, maintaining a steady arc and controlling the welding parameters, such as voltage, existing, and take a trip speed, assists develop a consistent weld swimming pool that minimizes the danger of gas entrapment. Using the right welding technique for the particular product being welded, such as changing the welding angle and gun position, can even more protect against porosity. Routine assessment of welds and immediate removal of any kind of problems recognized throughout the welding process are important methods to avoid porosity and generate top notch welds.
Significance of Proper Welding Techniques
Executing correct welding techniques is critical in guaranteeing the architectural integrity and top quality of welded joints, building on the structure of efficient porosity prevention steps. Welding methods directly impact the overall strength and longevity of navigate to these guys the welded framework. One key facet of appropriate welding techniques is preserving the right heat input. Extreme warmth can cause enhanced porosity as a result of the entrapment of gases in the weld pool. Conversely, inadequate warmth may result in insufficient fusion, producing potential powerlessness in the joint. In addition, utilizing the proper welding criteria, such as voltage, present, and take a trip rate, is essential for achieving audio welds with marginal porosity.
Moreover, the selection of welding procedure, whether it be MIG, TIG, or stick welding, should align with the certain demands of the task to make certain optimum results. Appropriate cleansing and preparation of the base steel, along with picking the ideal filler material, are likewise vital components of efficient welding strategies. By sticking to these ideal techniques, welders can decrease the danger of porosity development and produce premium, structurally audio welds.

Examining and Quality Control Measures
Quality assurance measures play a critical duty in verifying the stability and reliability of bonded joints. Evaluating procedures are necessary to find and avoid porosity in welding, making certain the strength and longevity of the last product. Non-destructive testing methods such as ultrasonic screening, radiographic testing, and visual examination are commonly used to determine potential flaws like porosity. These techniques enable for the evaluation of weld top quality without jeopardizing the stability of the joint. What is Porosity.
Post-weld examinations, on the other hand, examine the final click over here weld for any flaws, consisting of porosity, and confirm that it satisfies defined standards. Applying a comprehensive top quality control plan that consists of extensive screening procedures and examinations is vital to minimizing porosity concerns and making certain the overall high quality of bonded joints.
Conclusion
In conclusion, porosity in welding can be an usual issue that affects the top quality of welds. By recognizing the usual root causes of porosity and applying finest techniques for prevention, such as proper welding strategies view it now and testing measures, welders can make certain excellent quality and dependable welds. It is important to prioritize prevention methods to lessen the occurrence of porosity and maintain the stability of welded structures.
Report this page